Cleanroom Contamination Guide: What You Need to Know About Non-Viable Particles
- Ansac Team
- Jun 9
- 2 min read
Updated: Jun 24

In highly controlled environments such as pharmaceutical manufacturing, semiconductor fabrication, and electronics assembly, contamination can lead to disastrous consequences from failed audits and product recalls to equipment damage and yield loss.
Yet, many cleanroom professionals still underestimate one of the most persistent and invisible threats: Non-viable airborne particles.
In this guide, we break down:
What non-viable particles are
Why they matter in cleanroom operations
The standards that govern particle monitoring
Best practices for detection and control
What Are Non-Viable Particles?
Non-viable particles are inorganic contaminants such as dust, fibers, fumes, and metal fragments. Unlike viable particles (bacteria, fungi), non-viable particles do not carry microbial life but that doesn’t mean they’re harmless.
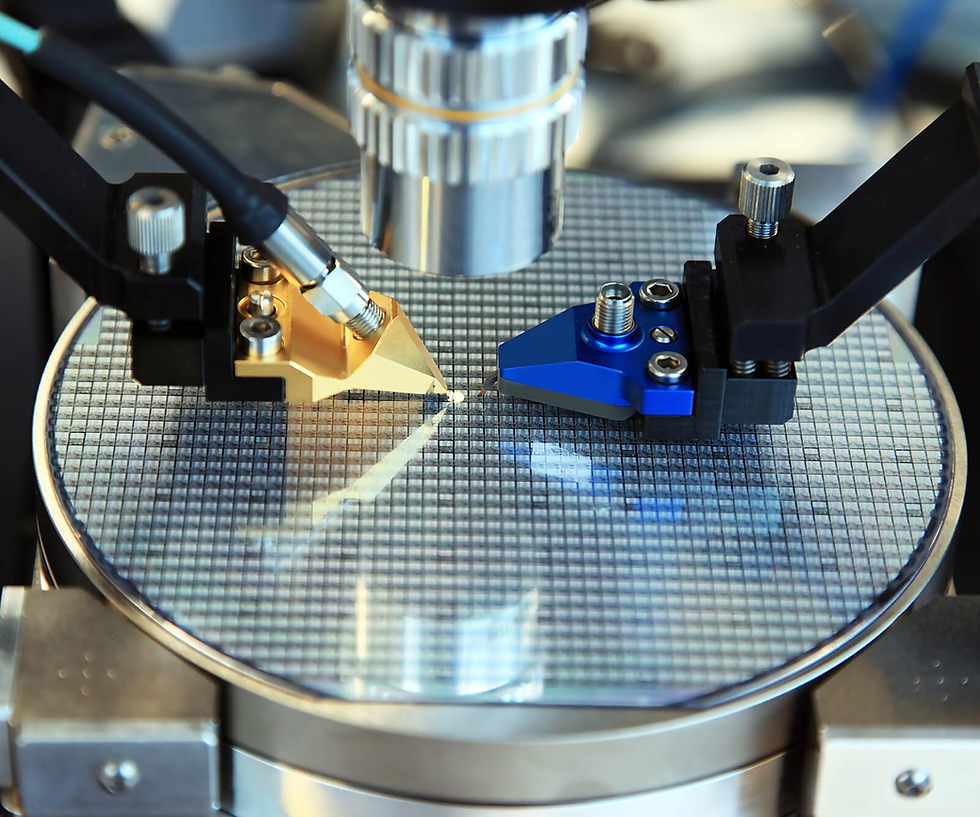
In fact, they:
Can act as carriers for microorganisms
Interfere with optical or electronic components
Compromise sterility in pharmaceutical environments
Cause physical defects in wafer production
Non-viable particles are measured in microns (µm) and are typically 0.3µm and above in cleanroom monitoring.
Why They Matter: Real World Impact

A semiconductor facility may lose hundreds of thousands of dollars from yield reduction due to airborne metal particles. A pharmaceutical line can be shut down over a single contaminated batch.
Even a short-lived excursion of particles in a cleanroom can:
Violate ISO Class 5 or 7 standards
Trigger a regulatory non-conformance
Lead to product batch rejection
Because these particles are invisible, fast-moving, and non-living, early detection and accurate monitoring are essential.
Particle Monitoring Standards to Know

Cleanroom particle monitoring is governed by international standards such as:
🔹 ISO 14644-1
Defines the maximum allowable particle concentration per cubic meter of air, segmented by cleanroom classes.
🔹 ISO 21501-4
Sets the calibration requirements for optical particle counters to ensure accurate and traceable measurement.
Facilities must regularly measure particle sizes like 0.3µm, 0.5µm, and 5.0µm, using properly calibrated instruments.
Best Practices for Non-Viable Particle Monitoring
Use ISO 21501-4 Compliant Counters Only use particle counters that meet international calibration standards for reliable data.
Supplement Fixed Counters with Portables Fixed systems monitor large spaces, but handheld and portable units allow spot checks in hard-to-reach or critical areas.
Establish Trending & Threshold Alerts Monitor for data spikes and use historical data to proactively address contamination risks.
Train Your Team on Data Handling Ensure staff understand sampling locations, data interpretation, and proper counter handling.
Schedule Routine Audits Regular internal audits help maintain ISO or GMP compliance and identify inefficiencies early.
CONCLUSION
Non-viable particles may be invisible, but their impact on your cleanroom operations is far from it.
Being proactive by understanding contamination risks, complying with global standards, and implementing the right monitoring tools is the best defense against costly cleanroom failures.
Want to Learn More?
Whether you’re just starting a monitoring program or looking to enhance your existing setup, we can help. Ansac Technology partners with leading brands to bring trusted contamination control solutions to industries like yours.
Comments